A recent study by Gartner predicts that by 2025, nearly 75% of organizations will use Digital Twin technology to improve their Product Lifecycle Management (PLM). Digital twins create virtual copies of physical products, systems, or processes, allowing businesses to monitor and manage them more efficiently throughout their entire lifecycle.
This technology enables companies to make informed decisions, reduce costs, and enhance product performance. For example, in the automotive industry, car manufacturers use digital twins to create virtual models of vehicles. These models help engineers test and improve the car’s performance, predict potential issues, and make adjustments before building the actual prototype.
By utilizing real-time data, digital twins provide valuable insights into every stage, from design to maintenance, enabling companies to optimize their products more effectively.
Here, we explained how digital twins are improving product lifecycle management.
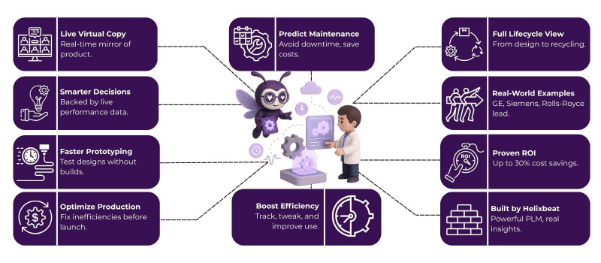
Table of Contents
What is a digital twin?
A digital twin is a virtual representation of a physical object, system, or process, created using real-time data. It mirrors the physical counterpart, enabling businesses to monitor their performance, behavior, and status continuously. This digital replica helps simulate different conditions, predict outcomes, and optimize processes without needing to directly interact with the physical asset.
Why is a Digital Twin Needed?
Product Lifecycle Management (PLM) requires digital twins because they offer several key benefits that help optimize the entire product journey:
- They provide real-time data, enabling businesses to monitor and analyze product performance continuously, leading to more accurate decisions.
- Digital twins enable the identification of potential issues before they occur, facilitating predictive maintenance that reduces downtime and extends product lifespan.
- By simulating various scenarios, digital twins help in design validation, enabling faster prototyping and reducing costly physical testing.
- They enhance collaboration across teams by providing a shared, up-to-date virtual model that integrates data from various departments, thereby improving decision-making.
- Digital twins enable businesses to gain a deeper understanding of and improve the efficiency of their processes, ultimately lowering operational costs and enhancing productivity throughout the product lifecycle.
Different Roles of Digital Twin?
Here’s how digital twins are making a difference across industries, especially in Product Lifecycle Management (PLM):
1. Tracking Performance in Real-Time: Digital twins enable businesses to continuously monitor assets, enhancing decision-making. For instance, 82% of manufacturers report improved efficiency with the real-time monitoring of turbines in the oil and gas sector.
2. Predicting Maintenance Before It’s Needed: By simulating product behavior, digital twins can predict when maintenance is needed, saving time and costs. McKinsey estimates predictive maintenance cuts costs by 30% and extends asset life by 20-40%, as seen in aviation with engine monitoring.
3. Testing Designs Without Building Them: Digital twins allow virtual testing, speeding up design and cutting costs. In aerospace, digital twins can reduce development time by 25% by simulating product performance before physical prototypes.
4. Making Processes More Efficient: By simulating real-world scenarios, digital twins help optimize operations. Siemens used them to improve plant energy efficiency by 10% and reduce production time by 20%.
5. Managing Products from Start to End: Digital twins track product performance throughout their lifecycle, helping plan maintenance and upgrades. General Electric uses them to monitor turbine lifecycles, improving efficiency and planning end-of-life replacements.
These roles highlight how digital twins add value at every stage of Product Lifecycle Management, offering insights and improving efficiency.
How Digital Twins Help in Product Lifecycle Management
Digital twins are transforming Product Lifecycle Management (PLM) by providing real-time, data-driven insights that improve decision-making, optimize product performance, and enhance efficiency. Here’s how digital twins contribute to PLM across different stages:
1. Enhancing Design and Prototyping Processes
Digital twins enable companies to create virtual prototypes and test them under different scenarios without building physical models. This helps streamline the design phase and reduce costly prototypes.
Example: In the aerospace industry, companies like Boeing use digital twins to simulate aircraft designs. By testing designs digitally before creating physical prototypes, they can detect potential issues earlier, reducing the time spent on physical testing by up to 25%. This accelerates product development and cuts costs associated with building and testing multiple prototypes.
Data: A McKinsey report found that using digital twins for early-stage design and prototyping could reduce product development time by up to 20%, leading to faster time-to-market.
2. Optimizing Manufacturing and Production
During the manufacturing phase, digital twins help improve operational efficiency by simulating real-world conditions and identifying process inefficiencies.
Example: Siemens uses digital twins to optimize the manufacturing process for gas turbines. By creating digital replicas of turbines, they can simulate different production scenarios and make adjustments in real-time to improve assembly line efficiency. This has led to a 10% increase in energy efficiency and a 20% reduction in production time.
Data: A study by PwC reveals that manufacturers using digital twins for process optimization report an average 15-20% improvement in operational efficiency, which significantly increases productivity while lowering costs.
3. Predicting Maintenance Needs and Reducing Downtime
One of the most significant advantages of digital twins is their ability to predict when maintenance will be needed. This helps prevent unexpected breakdowns and reduce downtime, ultimately extending product life.
Example: In the aviation sector, Rolls-Royce uses digital twins to monitor the health of aircraft engines. By collecting data from engines in flight, they create virtual models to predict maintenance requirements before any failure occurs. This proactive approach has reduced unplanned maintenance by 30%, improving aircraft availability and reducing operating costs for airlines.
Data: McKinsey reports that predictive maintenance using digital twins can reduce maintenance costs by up to 30% and extend asset life by 20-40%, resulting in substantial long-term savings.
4. Improving Product Performance and Efficiency
Digital twins offer valuable insights into product performance over time, enabling companies to pinpoint areas for improvement and make targeted adjustments to enhance product efficiency.
Example: General Electric (GE) uses digital twins in its wind turbine fleet to track performance data such as wind speed, vibration, and temperature. By continuously monitoring these factors, they can adjust turbine settings in real time to maximize energy output. This has resulted in a 5% increase in energy production from their turbines.
Data Insight: According to Accenture, companies using digital twins to optimize product performance report an average 10% improvement in energy efficiency and a 15% increase in overall product performance.
5. Supporting End-of-Life Decisions and Recycling
At the end of a product’s lifecycle, digital twins help businesses plan for product retirement, recycling, and reuse. By providing detailed insights into a product’s performance and remaining lifespan, digital twins assist in making informed decisions about repairs, replacements, or recycling.
Example: In the automotive industry, Tesla uses digital twins to track the lifespan of electric vehicle batteries. By analyzing data from the digital twin, Tesla can predict when batteries need replacement or maintenance, reducing waste and enhancing the recycling process.
Data Insight: Deloitte states that digital twins contribute to 50% more efficient asset management at the end of the product lifecycle, helping companies plan for recycling and reuse while reducing environmental impact.
Digital twins are revolutionizing Product Lifecycle Management (PLM) by enabling businesses to monitor, predict, and optimize every stage of a product’s life.
Example of Digital Twins in Industries
Digital twins are already transforming industries by providing real-time insights, enhancing operational efficiency, and enabling predictive maintenance.
1. General Electric (GE) – Aviation Industry
Application: GE uses digital twins to monitor and optimize the performance of aircraft engines. By creating a virtual replica of each engine, GE collects data from various sensors installed in the physical engine during flights, such as temperature, pressure, and vibration. This data is fed into the digital twin, where it is analyzed in real time to predict maintenance needs, detect potential failures, and optimize the engine’s performance.
Impact: By using digital twins, GE has been able to reduce unplanned downtime and improve engine reliability. This predictive maintenance approach has led to a 30% reduction in maintenance costs and a 20% increase in the lifespan of their engines.
Why Choose Helixbeat For Product Development
At Helixbeat, we provide easy-to-use Product Lifecycle Management (PLM) solutions that improve every part of your product’s journey. Using smart tools like digital twin technology, we give you real-time data to help you design better, produce faster, and predict maintenance before problems arise.
Our PLM software services help cut costs, increase efficiency, and speed up time-to-market. No matter what your industry, Helixbeat helps you make smarter decisions at every step, boosting product performance and profits. Book a free consultation with us.
FAQ:
1. What is Product Lifecycle Management?
Product Lifecycle Management (PLM) is the process of managing a product from its initial design through manufacturing, and up to its disposal. It integrates people, processes, and information to streamline development, reduce costs, and improve quality, ensuring efficiency and innovation at each product stage.
2. How to Choose a Digital Twin Development Company?
When selecting a digital twin development company, focus on their industry experience and expertise, as well as their ability to customize solutions to fit your needs. Ensure they use advanced technologies like IoT, AI, and machine learning, and provide continuous support and maintenance. It’s also essential to review their track record with case studies and customer testimonials to confirm they can deliver effective solutions.
3. What is Product Lifecycle Digital Twin?
A Product Lifecycle Digital Twin is a virtual model of a product that mirrors its physical counterpart across its entire lifecycle. This digital replica helps companies monitor performance, predict maintenance needs, and optimize design and manufacturing processes using real-time data, ultimately improving efficiency and decision-making.
4. What Are the Three Pillars of Digital Twin?
The three pillars of a digital twin are data, which comes from sensors and systems to reflect the current state of a physical asset; the model, which is the virtual replica that simulates the behavior and characteristics of the physical object; and connectivity, which integrates IoT, AI, and cloud computing for real-time data exchange between the physical and digital models.
5. Is Digital Twin an IoT?
While digital twins rely on the Internet of Things (IoT) for data collection, they are not the same. IoT connects devices to share data, while digital twins use that data to create a virtual model of a physical object. In essence, IoT provides the data, and the digital twin processes and simulates it for optimization and decision-making.