Did you know that more than 70% of oil and gas companies have already started using digital tools to improve their work? However, only about 3 out of 10 companies have successfully implemented these tools across their entire business. This shows that while many are trying, not all are fully prepared for the digital future.
The oil and gas industry is undergoing rapid change. It’s no longer just about digging for oil or running big machines. Now, it’s also about utilizing technology, such as smart sensors, cloud systems, and real-time data, to make better and faster decisions. This shift is enabling companies to transition from traditional working methods to smarter, more connected energy operations.
In this blog, we’ll explain why digital transformation in the oil and gas industry is so important today. We’ll also examine the common problems companies face, the significant benefits they can achieve, and real-world examples of how technology is already making a difference.
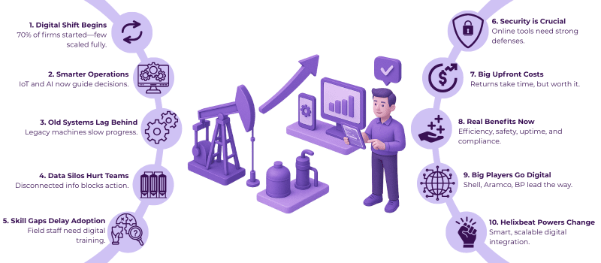
Table of Contents
Short note on Digital Transformation in the Oil and Gas Industry?
Digital transformation in the oil and gas industry refers to the application of advanced technologies, such as IoT, AI, data analytics, and cloud computing, to enhance the exploration, production, refining, and distribution of oil and gas. It helps reduce downtime, increase safety, cut operational costs, and make faster decisions using real-time data.
By transitioning from manual processes to digital systems, companies can remotely monitor equipment, predict failures before they occur, and manage energy resources more efficiently. This shift is not just about technology, it’s about building smarter, safer, and more sustainable operations across the energy value chain.
Key Challenges in the Digital Transformation of the Oil and Gas Industry
While digital transformation offers many benefits, energy companies face several key challenges during this shift. Here are five common obstacles explained in a simple and practical way:
1. Outdated Equipment and Legacy Systems
Many oil and gas operations still depend on old machines and systems that were not designed for digital use. Replacing or upgrading them takes time, money, and planning.
Example: A refinery using traditional pressure meters can’t send live data to a central system. To fix this, the company must install digital sensors, which adds cost and may cause temporary downtime.
2. Disconnected Data Across Departments
Data is often spread out across teams like drilling, production, and maintenance. Without connected systems, teams often work in silos, resulting in delays and suboptimal decisions.
Example: If the maintenance team can’t see equipment data from the drilling site, they might miss signs of wear and tear, resulting in unplanned breakdowns.
3. Limited Digital Skills in the Workforce
Oil and gas workers are skilled in field operations, but many lack experience with digital tools and data systems. Training the workforce is essential but takes time.
Example: A company may install an AI-based monitoring tool, but without trained staff to use it, the system won’t deliver its full value.
4. Cybersecurity Concerns
As more systems go online, the risk of cyberattacks increases. Protecting data and critical infrastructure becomes a top priority.
Example: In one well-known case, a cyberattack on a major pipeline led to fuel shortages, illustrating the vulnerability of digital systems when not properly secured.
5. High Initial Investment with Slow Returns
Digital upgrades often require large upfront costs. Some companies hesitate to invest because the financial benefits may not appear for some time.
Example: Installing IoT sensors on offshore rigs might cost millions. If improvements in efficiency or safety take longer than expected, decision-makers may question the value of the investment.
These challenges highlight the need for a smart, well-planned approach to digital transformation in the oil and gas industry. With the right strategy and support, companies can overcome these issues and build a more connected, efficient future.
Advantages of Oil & Gas Digital Transformation
Digital transformation is reshaping how oil and gas companies operate from drilling and refining to monitoring and maintenance. Here are four key benefits supported by industry data:
1. Improved Operational Efficiency
Digital tools like IoT sensors and real-time dashboards help companies monitor assets remotely, reduce delays, and optimize performance. For example, instead of sending crews to remote locations for equipment checks, teams can now track performance from a central control room saving time and reducing fuel and labor costs.
According to McKinsey, this shift can lower operating costs by 10–20% and increase production by up to 7%.
2. High Safety and Risk Management
Smart systems equipped with real-time alerts and remote sensing help detect dangers early, preventing accidents in hazardous environments. For instance, wearable devices can monitor a worker’s exposure to toxic gases and send instant alerts if levels become unsafe reducing risks without relying on manual checks.
A Deloitte study shows these digital safety tools can cut incident rates by up to 20%.
3. Predictive Maintenance and Less Downtime
AI-driven systems can analyze equipment data to predict failures before they happen, allowing timely maintenance and fewer unexpected breakdowns. For example, if sensors detect abnormal vibration in a compressor, maintenance can be scheduled before the issue worsens avoiding full-day shutdowns and saving money.
The World Economic Forum reports that predictive maintenance can reduce unplanned downtime by 30–50%.
4. Better Environmental Compliance and Sustainability
Digital solutions make it easier to track emissions, detect leaks, and manage energy use supporting both compliance and sustainability goals. In smart oilfields equipped with leak detection systems can spot and address gas leaks quickly, minimizing environmental damage and reducing fines.
According to Accenture, such tools can help cut greenhouse gas emissions by up to 15% in oil and gas operations.
A Step-by-Step Guide to Improve Digital Transformation in the Oil & Gas Sector
Digital transformation in the oil and gas industry works best when it’s approached with clear goals and operational alignment. Below are five focused steps tailored to energy companies looking to scale up their digital capabilities:
Step 1: Audit Field-Level Data Sources and Connectivity
Start by mapping your physical assets such as wells, rigs, pipelines, and processing units and identifying what data is being collected (if any) and how. Check for sensor availability, device health, and communication gaps between field instruments and central systems. Without reliable, real-time data at the asset level, no digital tool can offer value.
Example: In upstream operations, review the connectivity between wellhead sensors and SCADA systems. Are there delays, missing readings, or unsupported protocols? Fix these before adding advanced analytics.
Step 2: Prioritize Use Cases That Offer Measurable ROI
Instead of digitizing everything, focus on specific high-impact areas. Choose use cases that are tied directly to cost savings, safety improvement, or production gains.
Example: If you experience frequent pump failures, start with predictive maintenance on pumps instead of trying to implement plant-wide AI. This focus increases buy-in and gives teams confidence when results show up early.
Step 3: Build a Unified Data Infrastructure Across Upstream, Midstream, and Downstream
Oil and gas operations are often fragmented, with separate tools and data for exploration, transportation, and refining. Build a centralized data platform that brings these segments together using APIs and cloud integration.
Example: Use a platform that combines real-time pipeline data with storage tank levels and refinery performance. This integration allows supply chain teams to manage flow rates and reduce storage overflows or underutilization.
Step 4: Integrate Field Personnel with Digital Tools Through Mobile Interfaces
Even the best digital systems fail without adoption. Equip field teams with mobile apps or rugged tablets that show relevant data (alerts, manuals, digital forms) in real time. Don’t keep insights locked in the control room.
Example: Instead of calling the control room for pressure readings, field operators should access live data on their devices, confirm alarms, and log corrective actions digitally improving speed and traceability.
Step 5: Apply Layered Cybersecurity for All Connected Assets
As equipment and platforms become connected, the risk of cyberattacks increases. Implement layered security starting from device-level authentication to encrypted data transfer and continuous monitoring.
Example: Install access control protocols on field sensors, use VPNs for data transmission, and deploy intrusion detection tools that flag abnormal behavior like remote access attempts from unknown IPs.
Examples of Digital Transformation in Oil and Gas
1. Shell – AI for Predictive Maintenance
Shell uses machine learning and advanced analytics to predict equipment failures before they occur. By analyzing historical data from sensors on compressors, valves, and pipelines, Shell can identify patterns that signal a problem. This predictive maintenance approach has helped the company reduce unplanned downtime and lower maintenance costs across its global operations.
2. Saudi Aramco – Smart Oilfields with IoT
Saudi Aramco has implemented IoT-enabled smart oilfields that collect real-time data from thousands of field devices, including pressure sensors, flow meters, and temperature gauges. This data is analyzed using advanced software to optimize production, improve safety, and reduce manual inspections. As a result, field operations have become more efficient and cost-effective.
3. BP – Digital Twin Technology
BP uses digital twin technology to create virtual replicas of its physical assets like drilling platforms and refineries. These digital models simulate performance, predict failures, and test operational changes without disrupting actual systems. This has helped BP improve operational planning, reduce risks, and enhance asset reliability in complex environments.
Each of these examples shows how digital transformation in the oil and gas industry can lead to real efficiency gains, lower costs, and safer operations when technologies like AI, IoT, and digital twins are applied strategically.
Why Helixbeat is the Right Digital Partner for Oil & Gas
Digital transformation doesn’t have to be complex. With the right guidance, even the most traditional oil and gas operations can become smarter, safer, and more efficient. That’s where Helixbeat helps your transformation simple.
Helixbeat helps oil and gas companies move step by step from basic automation to advanced digital systems. Whether it’s connecting equipment in the field or utilizing real-time data to minimize breakdowns, Helixbeat develops solutions tailored to your needs and budget.
We bring all your systems together so that your data, teams, and technology work efficiently. And we don’t stop at setup; we support you throughout the journey with tools that grow as your operations grow.
If your company is wanting to move from manual work to modern, Helixbeat is ready to help. Start your digital transformation today with Helixbeat.
FAQ:
1. What is digital transformation in oil and gas?
Digital transformation in the oil and gas industry means using technology like sensors, data analytics, cloud platforms, and automation to improve how companies explore, produce, refine, and distribute oil and gas. It helps make operations faster, safer, more efficient, and better connected.
2. How has technology changed the oil and gas industry?
Technology has changed the oil and gas industry by enabling real-time monitoring, predictive maintenance, remote operations, and better decision-making. For example, companies now use smart sensors to track equipment performance and AI to predict failures before they happen, reducing downtime and increasing productivity.
3. Which industry has the most digital transformation?
The manufacturing, finance, and healthcare industries have seen the highest levels of digital transformation. However, the oil and gas sector is quickly catching up as companies invest in smart technologies to modernize operations and stay competitive.
4. What are the benefits of digitalization in the petroleum industry?
Digitalization in the petroleum industry brings many benefits, such as lower operational costs, improved safety, reduced equipment failures, faster decision-making, and better environmental compliance. It helps companies become more efficient and sustainable in the long run.
5. What is an example of a digital transformation?
A good example is when an oil company installs IoT sensors on its equipment to monitor performance in real time. These sensors send data to a central system, which uses AI to detect issues early. This helps prevent breakdowns and improves safety turning a traditional process into a smart, digital one.