Unplanned downtime costs industrial manufacturers over $50 billion annually, according to Deloitte. In high-throughput environments, even a brief halt in operations can result in significant revenue loss. This is where predictive maintenance (PdM) is making a measurable impact.
Using real-time sensor data, machine learning models, and historical equipment behavior, predictive maintenance allow manufacturers to detect failures before they occur. Unlike scheduled preventive maintenance, PdM is condition-based meaning repairs are carried out only when required, reducing unnecessary downtime and maintenance costs.
As part of the digital transformation in manufacturing, predictive maintenance integrates seamlessly with IoT and automation strategies in manufacturing. The result is greater equipment uptime and optimized performance. Let’s see how data analytics is saving manufacturers millions.
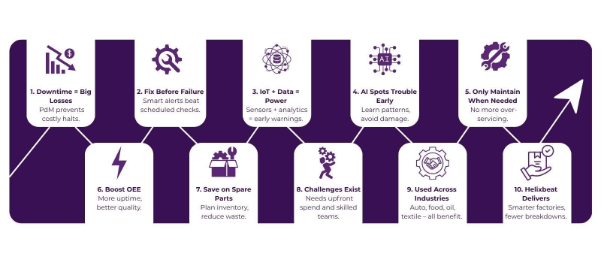
Table of Contents
What Is Predictive Maintenance?
Predictive maintenance (PdM) is a proactive maintenance strategy that uses data analytics, condition-monitoring technologies, and machine learning algorithms to identify potential equipment failures before they happen.
Today, predictive maintenance plays a central role in digital transformation in manufacturing, helping factories shift from manual, guess-based interventions to automated, data-driven decisions. It’s also a critical pillar of IoT in manufacturing, enabling continuous equipment monitoring across distributed production systems.
The Role of Data Analytics in Predictive Maintenance
In manufacturing, machine breakdowns can stop the entire production line. As a key part of digital transformation in manufacturing, predictive maintenance helps avoid this by using data to find problems early before the machine fails. Here’s how data analytics makes this possible on the factory floor:
1. Getting Data from Machines with IoT Sensors
Machines like motors, presses, and conveyors are fitted with IoT sensors that track things like temperature, vibration, and pressure. This information is sent to a central system, giving a clear view of how each machine is working.
2. Cleaning and Preparing the Data
The data from machines is often messy or incomplete. Special tools clean the data and organize it so it’s easy to read and use. For example, if a machine’s temperature keeps rising, that data is marked for attention.
3. Using Smart Models to Spot Problems Early
By looking at old machine data, smart algorithms learn what signs appear before something breaks. If similar signs are seen again like too much vibration or overheating, the system gives a warning before damage happens.
4. Helping Maintenance Teams Take Action
The system sends alerts to the maintenance team, telling them exactly which machine needs checking and when. This way, repairs happen during planned downtime, not during peak production hours—saving time and money.
Predictive Maintenance vs. Preventive Maintenance
Understanding the difference between predictive and preventive maintenance is essential for any business undergoing digital transformation in manufacturing, as it helps in choosing the right strategy to improve uptime and reduce costs.
Factor | Predictive Maintenance (PdM) | Preventive Maintenance (PM) |
Approach | Data-driven and condition-based | Time-based or usage-based schedule |
Use of Technology | Involves IoT sensors, machine learning, data analytics | Minimal tech; relies on manual checks or simple counters |
Maintenance Frequency | As needed, based on actual machine condition | Regular intervals, regardless of machine condition |
Cost Efficiency | Reduces unnecessary maintenance and avoids major failures | Can lead to over-maintenance and higher operational costs |
Downtime Impact | Minimizes unplanned downtime through accurate predictions | Reduces unplanned downtime but may still interrupt cycles |
Implementation Complexity | Higher – requires IoT, data infrastructure, skilled analysis | Lower – simple to schedule and execute |
Suitable For | High-value, critical assets or complex machinery | General use across non-critical assets |
Integration | Often integrated with CMMS, ERP, and industrial analytics tools | Typically standalone or minimally integrated |
Return on Investment (ROI) | High, especially in large-scale or automated production lines | Moderate, depends on asset type and failure rates |
How Predictive Maintenance Reduces Downtime and Saves Millions
Predictive maintenance (PdM) is no longer just a cost-saving tactic; it’s a strategic advantage for manufacturers. Here are five key ways PdM reduces downtime and delivers measurable financial impact:
1. Failure Prediction Through Real-Time Condition Monitoring
PdM uses real-time condition monitoring to track critical machine parameters like vibration, thermal output, lubrication levels, and RPM. This continuous data stream is analyzed against baseline performance thresholds.
If a parameter deviates from the expected range say a 10% spike in motor current an alert is triggered before mechanical failure occurs.
This level of proactive insight allows plant managers to intervene at the right time, avoiding catastrophic equipment breakdowns and production halts.
2. Optimized Maintenance Intervals Based on Asset Health
Traditional preventive maintenance often leads to over-maintenance, where parts are replaced before necessary, increasing cost without added value.
Predictive maintenance enables condition-based servicing, meaning work is done only when the data shows wear or degradation.
This reduces unnecessary part replacements, extends the lifespan of components, and frees up technician hours for higher-value tasks, all while reducing mean time between failures (MTBF) and improving mean time to repair (MTTR).
3. Minimizing Unplanned Downtime with AI-Based Forecasting
Using AI and machine learning algorithms, predictive maintenance systems analyze historical machine failures and production trends to forecast future issues.
For example, a machine learning model might detect that certain bearing temperature and vibration combinations typically precede gearbox failure within 72 hours.
Armed with this prediction, manufacturers can plan shutdowns during non-peak hours or batch production cycles, avoiding costly disruptions and missed delivery deadlines.
4. Inventory and Spare Parts Optimization
Because PdM provides clear insights into what will fail and when, manufacturers can better manage spare parts inventory. This reduces the need for overstocking expensive parts and prevents delays from not having the right component on hand when needed.
By integrating PdM data with ERP or CMMS systems, manufacturers can automate parts ordering and align maintenance schedules with parts availability, resulting in reduced carrying costs and improved procurement efficiency.
5. Improved Overall Equipment Effectiveness (OEE)
Predictive maintenance directly impacts all three pillars of Overall Equipment Effectiveness (OEE): availability, performance, and quality.
Fewer unplanned stoppages improve equipment availability, timely servicing maintains peak performance, and well-maintained machines produce higher-quality outputs.
A 2023 report by McKinsey shows that plants using predictive maintenance effectively can increase OEE by up to 20%, translating into millions in annual productivity gains for large-scale manufacturing operations.
Challenges Manufacturers Face While Adopting Predictive Maintenance
Predictive maintenance can transform how manufacturers manage machine health, but adopting it comes with a few challenges. Understanding these early can help avoid delays, overspending, or poor outcomes.
1. High Initial Investment
Getting started with predictive maintenance requires spending on IoT sensors, data infrastructure, cloud platforms, and sometimes upgrading old equipment. This can seem costly, especially for small or mid-sized factories. However, this investment pays off over time by preventing major breakdowns, reducing downtime, and lowering maintenance costs.
2. Need for Skilled Workforce
Predictive maintenance isn’t just about sensors—it also needs people who understand data analysis, machine behavior, and maintenance software. Existing staff may need upskilling, or companies may have to hire data specialists and engineers familiar with AI or machine learning. Without the right skills, the system won’t deliver accurate insights.
3. Data Quality and Integration Problems
If the data collected from machines is inconsistent, incomplete, or delayed, the predictions won’t be accurate. Many older machines also aren’t designed to share data easily, so integrating them into a central system can be tough. Good data hygiene, sensor calibration, and system integration are key to success.
4. Cybersecurity and Data Privacy Risks
As factories connect machines to the internet or cloud (via IoT in manufacturing), the risk of cyberattacks increases. Hackers could target your systems, steal data, or disrupt production. Manufacturers need to invest in cybersecurity measures, like encrypted networks, firewalls, and regular audits to keep systems safe.
Use Cases of Predictive Maintenance Across Industries
Predictive maintenance is helping various industries avoid costly breakdowns and improve efficiency. Here are four examples:
1. Automotive Manufacturing: Robot arms used in assembly lines are monitored for vibration, torque, and heat. Predictive models detect early signs of wear, preventing sudden failures during production.
2. Food and Beverage: Refrigeration units are critical for food safety. Sensors track compressor performance, allowing early intervention before cooling failure leads to product spoilage.
3. Oil and Gas: Pumps and valves in remote locations are monitored for pressure and temperature changes. Predictive analytics help prevent leaks and costly shutdowns.
4. Textile Industry: Spinning and weaving machines are tracked for belt tension and motor load. Maintenance is scheduled before breakdowns, reducing downtime and quality issues.
Final Thoughts: Make Predictive Maintenance Work for You
Predictive maintenance enables manufacturers to avoid unexpected breakdowns, minimize repair costs, and maintain machine efficiency. By using real-time data and smart tools, you can fix problems before they stop your production and save a lot of money in the process.
But to make it work, you need the right technology and the right partner.
Helixbeat makes it easy to bring predictive maintenance into your factory as part of a complete digital transformation in manufacturing. We help you set up IoT sensors, connect your machines, and turn your data into actionable insights, all tailored to your specific operations.
If you want fewer breakdowns, better productivity, and higher profits, get in touch with Helixbeat today. Let’s build a smarter, more efficient factory together.
FAQ:
1. What is digital transformation in manufacturing?
Digital transformation in manufacturing involves utilizing digital technologies, such as IoT, automation, AI, cloud platforms, and data analytics, to enhance the operational efficiency of factories. It helps manufacturers monitor machines in real-time, reduce downtime, improve product quality, and make faster decisions using data.
2. What are the benefits of digital transformation in manufacturing?
Digital transformation helps reduce operational costs by automating tasks and improving efficiency. It lowers unplanned downtime through real-time machine monitoring. It also enhances production quality and provides managers with real-time insights for informed decision-making. Overall, it increases competitiveness and speeds up innovation.
3. What is the digital transformation roadmap for the manufacturing industry?
The roadmap begins by assessing the current systems and defining clear digital goals. The next step is installing IoT sensors to gather machine data. This data is then used through analytics and AI to improve operations. Manufacturers also automate manual tasks and integrate systems for better workflow. Lastly, they train their teams and scale the digital strategy across all units.
4. What are the three major aspects of digital manufacturing?
The first aspect is connectivity, which links machines, systems, and data using IoT and cloud platforms. The second is automation, where robots and smart software take over repetitive tasks. The third is intelligence, which involves using data analytics and machine learning to gain insights and improve decision-making.
5. What is the main goal of digital transformation?
The main goal is to make manufacturing smarter, faster, and more cost-effective by using technology. It helps companies stay competitive, reduce waste, and respond quickly to market demands.