For manufacturers, staying efficient and cutting costs are top priorities. One way companies are achieving this is through predictive maintenance, a smart approach that uses data and technology to predict when machines might fail. This helps businesses fix problems before they happen, preventing expensive downtime and repairs.
Research shows that predictive maintenance can cut unplanned downtime by up to 50%, saving manufacturers millions of dollars. By using real-time data, this method helps companies run smoothly, take better care of their equipment, and avoid unexpected breakdowns.
As part of the broader digital transformation in manufacturing, predictive maintenance is a key step in improving efficiency and achieving long-term goals. To avoid costly machine problems, more manufacturers are choosing predictive maintenance as a smarter, money-saving solution. Let’s see the details about digital transformation in manufacturing.
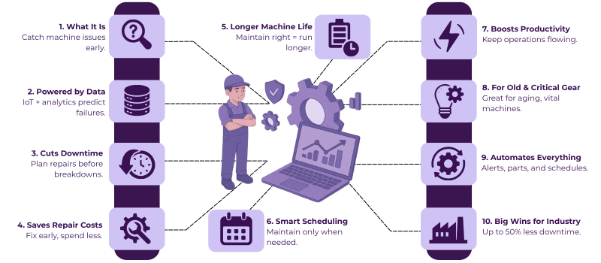
Table of Contents
What is Predictive maintenance in Manufacturing
Predictive maintenance is a strategy employed in manufacturing to anticipate when equipment or machines may fail, allowing for preventive maintenance to be performed before a problem arises. Instead of waiting for something to break down, sensors and data are used to monitor the machines. These sensors collect information like temperature, vibration, and pressure. This data is then analyzed to identify any unusual patterns that might suggest a future failure.
By knowing in advance when maintenance is needed, manufacturers can plan repairs during non-production times, avoiding costly unplanned downtime. Predictive maintenance enables businesses to save money, extend the lifespan of their equipment, and maintain smooth operations.
The Role of Data Analytics and IoT in Predictive Maintenance
Data analytics and IoT play a crucial role in predictive maintenance by enabling real-time monitoring and data-driven insights, which are essential components of digital transformation in manufacturing.
Data Analytics in Predictive Maintenance
Data analytics plays a crucial role in predictive maintenance by processing and analyzing the vast amounts of data collected from machines. With the help of data analytics, manufacturers can spot patterns and trends that might indicate potential issues, even before they happen.
By analyzing data such as machine performance, temperature, vibration, and other key metrics, businesses can predict when a machine is likely to fail or need maintenance.
Example:
If a machine’s temperature steadily increases beyond normal levels over time, data analytics can detect this trend and alert operators that maintenance is needed before the machine actually breaks down. This helps avoid sudden disruptions and costly repairs, ensuring smooth and continuous operations.
IoT in Predictive Maintenance
The Internet of Things (IoT) involves connecting machines and equipment to the internet, allowing them to send real-time data to a central system for monitoring and analysis. In predictive maintenance, IoT devices such as sensors are placed on machinery to track its condition continuously.
These sensors collect valuable information like vibrations, pressure, and temperature, which is then sent to a cloud-based system for analysis.
Example:
In an automotive factory, IoT sensors can be installed on robotic arms to monitor their movement and performance. If the sensors detect unusual vibrations or movements, an alert is triggered, allowing technicians to inspect and fix the issue before the robotic arm breaks down. This integration of IoT makes predictive maintenance smarter and more efficient, reducing unplanned downtime and increasing productivity.
How Predictive Maintenance Saves Manufacturers Millions
By incorporating predictive maintenance, manufacturers can reduce costly downtime, extend the life of their equipment, and cut repair expenses, all of which are key benefits of digital transformation in manufacturing.
1. Reduces Unplanned Downtime:
- Predictive maintenance helps identify potential issues before they cause machine breakdowns. By predicting when maintenance is needed, businesses can schedule repairs during non-production hours, preventing unexpected downtime that can disrupt operations and lead to lost revenue.
- Studies show predictive maintenance can reduce unplanned downtime by up to 50%, resulting in significant savings.
2. Lowers Repair Costs
- Addressing issues early with predictive maintenance reduces the need for costly emergency repairs. By catching problems before they escalate, manufacturers avoid expensive breakdowns and expensive last-minute parts replacement.
- Predictive maintenance has been shown to reduce repair costs by up to 25-30%, lowering overall maintenance expenditures.
3. Extends Equipment Lifespan
- By continuously monitoring machine health and performing timely maintenance, equipment lasts longer. This reduces the need for early replacements and helps maximize the value of each asset, saving manufacturers significant costs on capital expenditures.
- With predictive maintenance, equipment lifespan can be extended by up to 40%, delaying costly replacements.
4. Optimizes Maintenance Schedules
- Instead of performing routine maintenance at set intervals, predictive maintenance ensures that maintenance is only carried out when necessary. This reduces unnecessary maintenance work, lowers labor costs, and improves overall efficiency in the manufacturing process.
- Predictive maintenance has been found to reduce maintenance labor costs by 20-25%, allowing for more efficient resource allocation.
5. Improves Productivity and Efficiency
- With predictive maintenance in place, manufacturers can ensure that equipment operates at peak performance. This increases overall productivity and reduces delays caused by faulty equipment, resulting in higher output and better profitability.
- Implementing predictive maintenance can boost productivity by 10-20%, leading to higher operational efficiency and improved profit margins.
When Does Your Business Need Predictive Maintenance?
Implementing predictive maintenance is a key part of digital transformation in manufacturing, helping businesses reduce downtime, cut maintenance costs, and extend equipment life.
1. Frequent Equipment Breakdowns
If your business experiences frequent equipment breakdowns or downtime, it’s a clear sign that predictive maintenance could benefit you. Predictive maintenance helps you identify issues before they cause equipment failures, reducing unexpected downtime.
Example: In a manufacturing plant, if machines are constantly breaking down, leading to production delays, predictive maintenance can monitor equipment health and alert operators before problems occur, reducing downtime significantly.
2. High Maintenance Costs
If your maintenance costs are consistently high due to reactive repairs or frequent equipment replacements, predictive maintenance can help lower these expenses. By predicting failures in advance, you can reduce the need for expensive emergency repairs and unnecessary replacements.
Example: A factory that regularly replaces parts or calls in emergency repair services due to unplanned failures can switch to predictive maintenance to only replace parts when they are truly needed, saving money on unplanned expenses.
3. Old Machinery
Older machinery is more prone to breakdowns. If your business relies on aging equipment, it’s especially important to implement predictive maintenance. This will help you catch potential failures early and prevent costly breakdowns that could disrupt your operations.
Example: An automotive assembly line with older robotic arms can benefit from predictive maintenance to monitor their performance and predict wear and tear, allowing for repairs before a critical failure occurs.
4. Complex or Critical Machines
If your business uses complex or critical machinery that directly impacts production, predictive maintenance is essential. With advanced equipment, a small failure can lead to significant disruptions. Predictive maintenance helps you keep these machines running smoothly by detecting issues early.
Example: In the oil and gas industry, where machinery failure can have serious financial and safety implications, predictive maintenance can monitor pumps and compressors to predict problems and schedule repairs without halting operations.
Using Predictive Maintenance to Automate Manufacturing
- Real-Time Monitoring and Alerts: Predictive maintenance uses sensors to monitor equipment in real-time and send automatic alerts for potential issues, enabling quick, automated responses to prevent damage.
- Automated Maintenance Scheduling: It automatically schedules maintenance based on data insights, reducing manual intervention and ensuring timely repairs.
- Inventory and Parts Management: Predictive maintenance tracks part conditions and reorders components automatically, ensuring essential parts are always in stock.
- Optimized Machine Usage: It adjusts machine operations based on real-time data, preventing overuse and extending equipment life.
- Enhanced Production Workflow: Integrating predictive maintenance with other automated systems streamlines production, reducing downtime and improving efficiency.
Final Words
At Helixbeat, we help manufacturers go digital, so their work becomes easier, faster, and more affordable. We utilize tools such as IoT, data analytics, and predictive maintenance to enhance machine performance, minimize downtime, and automate routine tasks.
We know that every business faces different challenges, so we provide customized solutions to meet your specific needs. Whether it’s improving production, increasing machine reliability, or cutting maintenance costs, we are here to help you reach your goals.
With digital transformation in manufacturing, we guide businesses in using technology to work smarter and achieve better results. Let’s optimize your manufacturing process. Book a free consultation now.
FAQ:
1. Short note on digital transformation in manufacturing
Digital transformation in manufacturing involves using technologies like IoT, data analytics, and automation to enhance production, reduce costs, and improve efficiency. It enables real-time data use for smarter decision-making and greater agility in manufacturing processes.
2. What is one benefit of data analysis in manufacturing?
One major benefit of data analysis in manufacturing is predictive maintenance. By analyzing data from machines, manufacturers can predict when a machine is likely to fail, allowing them to perform maintenance before a breakdown occurs, reducing downtime and repair costs.
3. Why is manufacturing data important?
Manufacturing data is important because it provides insights into the performance of machines, products, and processes. This data helps businesses make informed decisions, optimize operations, improve product quality, and reduce waste, leading to cost savings and greater competitiveness.
4. Importance of automation in manufacturing
Automation in manufacturing increases production speed, consistency, and accuracy while reducing human error and labor costs. It helps businesses maintain a high level of productivity, improves product quality, and ensures more efficient use of resources, leading to overall cost savings and improved profitability.
5. Role of IoT in manufacturing
IoT (Internet of Things) in manufacturing connects machines and equipment to the internet, enabling real-time monitoring and data collection. This helps manufacturers track performance, detect faults early, and make adjustments automatically, improving efficiency, reducing downtime, and enhancing decision-making processes.